Saturday, November 11, 2006
It's Done!
Here is the finished guitar (outside in January -- I love San Diego).


This was a very rewarding project. I learned a lot that I couldn't have learned by just reading about it. The guitar doesn't play like an expensive guitar, but it was certainly worth my time. Besides, it'll make a nice conversation piece hanging over my fireplace.
For those of you following this project from the start you may have noticed a lack of updates for the past couple of months. After finishing the project my enthusiasm to update this page waned. It wasn't until I got an enthusiastic e-mail from a guy named Paul who was just about to start the same kit that I finally got it in gear and finished this page. Thanks, Paul.
This project is finished. Now I'm searching for another...




This was a very rewarding project. I learned a lot that I couldn't have learned by just reading about it. The guitar doesn't play like an expensive guitar, but it was certainly worth my time. Besides, it'll make a nice conversation piece hanging over my fireplace.
For those of you following this project from the start you may have noticed a lack of updates for the past couple of months. After finishing the project my enthusiasm to update this page waned. It wasn't until I got an enthusiastic e-mail from a guy named Paul who was just about to start the same kit that I finally got it in gear and finished this page. Thanks, Paul.
This project is finished. Now I'm searching for another...
Final Assembly
No more painting! No more sanding! No more waiting for things to dry! Smooth sailing from here! Yeah, right.
Bolting on the neck seems like a trivial task. Technically, it should be. Either the wood had swelled or the finish inside the neck pocket built up too much. In either case this was not an exercise in finesse. In hind sight I should have sanded down the sides of the neck pocket until the neck went in snugly, but easily. As it was I pretty much jammed it in there and used to neck screws to snug it down. I'm lucky I didn't break anything. I really wanted a black neck plate but I couldn't find one before I decided to mount the neck. Now it's never coming off! Notice the reflection of the light reveals an uneven surface. This is what happens when you don't use enough sanding sealer.

Well, at least the big stuff is done. Now I'll just hook up some wires and start playing! As if.
It turns out that the pockets for the pickups don't fit the pickups (why didn't I test this earlier?). The neck pickup fit particularly poorly but there was little I could do about that one. I just use a rat tail file to open up the corners of the pockets a bit and managed to get the pickups in. This would have been a lot easier before the body was finished.

My enthusiasm still intact I installed the bridge and tuners. Remarkably, this went extremely smoothly despite the fact that installing the studs for the bridge required using a hammer (I wasn't forcing it, that's just the way you do it!). I test-fit the tuners and marked where to drill pilot holes for the set screws. At first I tried it without the holes but those tiny screws are difficult to get into that very hard wood.

Installing the rest of the wiring and various bits and pieces was trivial. There were two screws missing for the back cover, but it fit snugly enough to not worry about it. However, I did notice that the holes didn't line up correctly -- something else I should have fixed earlier. After that I put on the strings, tuned it up and started to jam...
Hindsight:
Bolting on the neck seems like a trivial task. Technically, it should be. Either the wood had swelled or the finish inside the neck pocket built up too much. In either case this was not an exercise in finesse. In hind sight I should have sanded down the sides of the neck pocket until the neck went in snugly, but easily. As it was I pretty much jammed it in there and used to neck screws to snug it down. I'm lucky I didn't break anything. I really wanted a black neck plate but I couldn't find one before I decided to mount the neck. Now it's never coming off! Notice the reflection of the light reveals an uneven surface. This is what happens when you don't use enough sanding sealer.

Well, at least the big stuff is done. Now I'll just hook up some wires and start playing! As if.
It turns out that the pockets for the pickups don't fit the pickups (why didn't I test this earlier?). The neck pickup fit particularly poorly but there was little I could do about that one. I just use a rat tail file to open up the corners of the pockets a bit and managed to get the pickups in. This would have been a lot easier before the body was finished.

My enthusiasm still intact I installed the bridge and tuners. Remarkably, this went extremely smoothly despite the fact that installing the studs for the bridge required using a hammer (I wasn't forcing it, that's just the way you do it!). I test-fit the tuners and marked where to drill pilot holes for the set screws. At first I tried it without the holes but those tiny screws are difficult to get into that very hard wood.


Installing the rest of the wiring and various bits and pieces was trivial. There were two screws missing for the back cover, but it fit snugly enough to not worry about it. However, I did notice that the holes didn't line up correctly -- something else I should have fixed earlier. After that I put on the strings, tuned it up and started to jam...
Hindsight:
- Test fit everything first. Trimming the neck and pickup pockets would have been easier if I didn't have to worry about the finish.
- Be very careful when installing hardware. One slip of a screwdriver can gouge that beautiful finish (not mine fortunately).
- Don't be stingy with the sanding sealer. Not only will it look better at this point but it'll minimize the chance of sanding through.
Finish Sanding and Rubbing Out
Ok, the spraying is done. I used three cans of gloss clear coat and a bit of satin clear coat for the back of the headstock. Now it's time for the final sanding (Ugh).
I soaked several grits of wet sandpaper in water for several hours. The idea is to spend as much time as possible with the coarse grits to save time with the finer grits. However, I went the cautious route and spent most of my time (and effort) with the finer grits. At first the finish became cloudy but the finer grades started to bring out the shine. I rinsed the paper often and tried to keep the water out of the unpainted holes where it could swell the wood and crack the finish.
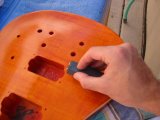
Rubbing out is just the insiders way of saying polishing. As per the suggestions at the Guitar ReRanch I used 3M Finesse-It II for rubbing out. It recommends using a machine, but Mark Power would have to do. Now I'll be able to see if all of this effort has paid off.

After another half hour or so of rubbing (my arms were aching at this point) the body and headstock were shining like a mirror. I know it just looks like an orange guitar in the pictures but they can't convey the subtlety of the way the light plays with the grain. There is even more depth and glow than I had expected.

Tips:
I soaked several grits of wet sandpaper in water for several hours. The idea is to spend as much time as possible with the coarse grits to save time with the finer grits. However, I went the cautious route and spent most of my time (and effort) with the finer grits. At first the finish became cloudy but the finer grades started to bring out the shine. I rinsed the paper often and tried to keep the water out of the unpainted holes where it could swell the wood and crack the finish.
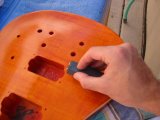
Rubbing out is just the insiders way of saying polishing. As per the suggestions at the Guitar ReRanch I used 3M Finesse-It II for rubbing out. It recommends using a machine, but Mark Power would have to do. Now I'll be able to see if all of this effort has paid off.

After another half hour or so of rubbing (my arms were aching at this point) the body and headstock were shining like a mirror. I know it just looks like an orange guitar in the pictures but they can't convey the subtlety of the way the light plays with the grain. There is even more depth and glow than I had expected.


Tips:
- Take your time. Rushing here would only mess up weeks of work.
- Sanding is just to get the finish ready for polishing -- don't worry about shine until the last step.
- Be wary of sanding the edges! Even very fine grits can get through all those clear coats (trust me).
Clear Coating the Body
This step is easy: Spray on a whole bunch of clear lacquer and BAM! you've got a beautiful guitar. Ok, perhaps it's not that simple. To prove this fact I launched a few large droplets of clear coat onto the face of the body to mar an otherwise beautiful finish. This happened after I'd already applied a couple of coats of clear so it's not as bad as it could have been. I let it dry overnight because I knew there was only one way to fix it and I wasn't looking forward to it.

The only way to fix this involved my arch-nemesis: sanding. I used a finer grade of sandpaper than I'd used in the sanding sealer fiasco. I wrapped it around a 9-volt battery and *gently* sanded the area around the droplets. For good measure (and to tempt the Fates) I decided to scuff sand the entire body.
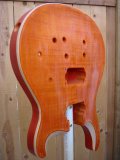
The sanding went much better than it had before but I did manage once again to sand off a bit of color. This time it shows as a yellow spot on the face of the guitar. I used my full-strength dye mixture to patch the spot. You may have trouble seeing the flaw in the small picture but it jumps out to my eye. By the way, I really should be wearing gloves here...

The patch was fairly successful. I may be the only one who still thinks it's flawed. The first few coats I added were very thin. I've started slowing down my spray passes to build the thickness. After a few coats of clear the finish is really looking good!

Things to remember:

The only way to fix this involved my arch-nemesis: sanding. I used a finer grade of sandpaper than I'd used in the sanding sealer fiasco. I wrapped it around a 9-volt battery and *gently* sanded the area around the droplets. For good measure (and to tempt the Fates) I decided to scuff sand the entire body.

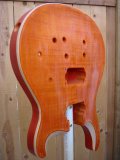
The sanding went much better than it had before but I did manage once again to sand off a bit of color. This time it shows as a yellow spot on the face of the guitar. I used my full-strength dye mixture to patch the spot. You may have trouble seeing the flaw in the small picture but it jumps out to my eye. By the way, I really should be wearing gloves here...

The patch was fairly successful. I may be the only one who still thinks it's flawed. The first few coats I added were very thin. I've started slowing down my spray passes to build the thickness. After a few coats of clear the finish is really looking good!

Things to remember:
- I can't sand over color to save my life. Avoid this at all cost on future projects.
- Using a finer grade of sand paper was a good idea.
- Add clear coat in slow, smooth motions. Not enough lacquer builds up with fast passes.
Dyeing the Headstock
One day while inspecting the headstock I noticed that the pre-drilled holes for the truss rod cover were not centered. This will not do! I applied some wood filler and let it dry for a few hours.

In the mean time I masked off the face of the headstock and sealed the edges with a couple coats of clear. Since I'm only dying the front of the headstock I wanted to make sure it would be easy to scrape off any dye that got onto the sides.

After the clear coat dried overnight I removed the masking, drilled the new holes for the truss rod cover (rather poorly I might add) and masked the edges in preparation for the dye.

I layered the yellow and orange dye in the same manner as I had for the body. After it dried I removing the masking and scraped the edges with an X-Acto knife to keep them nice and clean. Since the headstock is made of different wood than the body the color is slightly different. It looks bland to me, but I'm sure it'll work after the clear coats and all the black hardware is installed.

In the same weekend the lengthy task of clear coating began. Since I get home too late to work in the evenings this is turning into a three weekend task. Also, not to let any job be too simple I've decided to use clear gloss on the face and clear satin on the back and sides.

Lessons:

In the mean time I masked off the face of the headstock and sealed the edges with a couple coats of clear. Since I'm only dying the front of the headstock I wanted to make sure it would be easy to scrape off any dye that got onto the sides.

After the clear coat dried overnight I removed the masking, drilled the new holes for the truss rod cover (rather poorly I might add) and masked the edges in preparation for the dye.

I layered the yellow and orange dye in the same manner as I had for the body. After it dried I removing the masking and scraped the edges with an X-Acto knife to keep them nice and clean. Since the headstock is made of different wood than the body the color is slightly different. It looks bland to me, but I'm sure it'll work after the clear coats and all the black hardware is installed.

In the same weekend the lengthy task of clear coating began. Since I get home too late to work in the evenings this is turning into a three weekend task. Also, not to let any job be too simple I've decided to use clear gloss on the face and clear satin on the back and sides.

Lessons:
- Wood filler is softer than wood so be careful drilling on seams of filler and wood.
- Make sure to sand off the sealer all the way to the nut. I left a little and it shows when dyeing.
Applying the Sanding Sealer
I needed a way to hold the guitar while spraying the sealer. My Stack-O-Wood wouldn't work here since I would be spraying all sides at once. After a quick trip to Home Depot I fashioned a handle from some PVC and a couple of screws. Following the walkthrough I added a shim under the handle to allow the sealer to get into the neck cavity.

The spraying was pretty uneventful. Two coats per day for two days. I soaked the tip of the spray can in lacquer thinner between coats to keep it flowing smoothly.

I sanded down the body by wrapping 220 grit sandpaper around a 9 volt battery. Unfortunately I was a bit overzealous and sanded through the paint in several places. Gah! This is how wisdom is earned.

I thinned out the orange dye I'd used for the body and used a cotton swab to repair the damage. This worked well in some places and not so well in others. Notice I'm wearing gloves -- I'm also wearing goggles.

Wisdom earned:


The spraying was pretty uneventful. Two coats per day for two days. I soaked the tip of the spray can in lacquer thinner between coats to keep it flowing smoothly.


I sanded down the body by wrapping 220 grit sandpaper around a 9 volt battery. Unfortunately I was a bit overzealous and sanded through the paint in several places. Gah! This is how wisdom is earned.


I thinned out the orange dye I'd used for the body and used a cotton swab to repair the damage. This worked well in some places and not so well in others. Notice I'm wearing gloves -- I'm also wearing goggles.

Wisdom earned:
- Get a portable workbench. Seriously.
- The handle works well (and 10 ft of 3/4" PVC only costs $1).
- Check the sandpaper for signs of color. Often. Extra minutes spent here will save you hours later.
- Roll the cotton swab, don't rub. The dye contains thinner which is very effective for removing dye.
- Layered dyes don't patch well when sanded through. Grrr.