Wednesday, July 27, 2005
Shaping the Headstock
A nice feature of the Saga kit is that the headstock comes as a simple paddle giving me the opportunity to customize it. I cut out a cardboard template and cut out a few designs. After much deliberation I decided on one and traced the pattern onto the headstock.

After a futile attempt to file down the wood I cut off the majority with a small hand saw. Filing down the shape from there was much easier. I carefully filed the bevel onto one side of the pattern per my drawing. The blue tape is to prevent the non-beveled side from getting marred.

The file pulled off a few small chips which I filled with wood putty.

I'm pretty pleased with the results. I'll be dyeing the face of the headstock to match the body leaving the edges (including the bevel) natural like the cutouts in the body. Oh good. More masking.

Notes to self:



After a futile attempt to file down the wood I cut off the majority with a small hand saw. Filing down the shape from there was much easier. I carefully filed the bevel onto one side of the pattern per my drawing. The blue tape is to prevent the non-beveled side from getting marred.



The file pulled off a few small chips which I filled with wood putty.

I'm pretty pleased with the results. I'll be dyeing the face of the headstock to match the body leaving the edges (including the bevel) natural like the cutouts in the body. Oh good. More masking.


Notes to self:
- Cardboard template was a good idea.
- Get a portable workbench and a vice.
- Sawing is faster than filing.
- Slow down that filing mister! Chips can be avoided.
Dyeing the Back and Sides
The body of the guitar is basswood. I considered just painting it black but in the end (because I didn't have any black paint) decided to use the same layering technique I had on the front. I wouldn't use a pre-dye though.
After one aborted attempt at masking off the top I started over using a paper cut out to cover the top first. Masking is more important this time since it has to protect the color on the top. I masked the top and the natural binding. This was a lot more work than making the sides.

After setting up my paint booth again (a week has past and I wasn't going to keep parking in the driveway) I was ready to dye again. This time I set up a variant of the Stack-O-Wood called the Pile-O-Wood specifically engineered for painting the sides of the body.

Here is the body in the early stages of dyeing and after it's done. I waited a minimum of five minutes between coats. Even though I used a lot of yellow the basswood dyed darker than the maple. It was hard to compare the colors since the top was masked off.

Peeling off the masking revealed a beautifully contrasting natural binding. And in a time-consuming but entertaining effort I got the entire masking off in one piece.

I applied my engineering background to construct a drying mechanism from available furniture and a wire coat hanger.

Here is the final color on the body. This is turning out so well I'm already starting to think of my next project...

Here are some time consuming lessons I'll keep in mind.
After one aborted attempt at masking off the top I started over using a paper cut out to cover the top first. Masking is more important this time since it has to protect the color on the top. I masked the top and the natural binding. This was a lot more work than making the sides.

After setting up my paint booth again (a week has past and I wasn't going to keep parking in the driveway) I was ready to dye again. This time I set up a variant of the Stack-O-Wood called the Pile-O-Wood specifically engineered for painting the sides of the body.

Here is the body in the early stages of dyeing and after it's done. I waited a minimum of five minutes between coats. Even though I used a lot of yellow the basswood dyed darker than the maple. It was hard to compare the colors since the top was masked off.
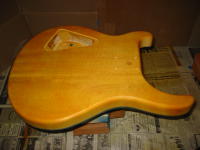

Peeling off the masking revealed a beautifully contrasting natural binding. And in a time-consuming but entertaining effort I got the entire masking off in one piece.
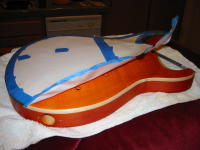

I applied my engineering background to construct a drying mechanism from available furniture and a wire coat hanger.

Here is the final color on the body. This is turning out so well I'm already starting to think of my next project...
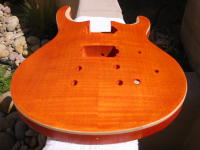

Here are some time consuming lessons I'll keep in mind.
- Don't build a wall of masking tape around the sides of the body then try to fill it in. Just make a paper cut out of the top and tape it down.
- Do not spray in upward strokes. This causes droplets to splatter on the newly dyed surface. Lightly rubbing with a rag slightly damp with lacquer thinner blended in the drops. Act fast though, it evaporates quickly.
- I should have marked the bottom of the binding before masking the natural binding. I over masked the binding making it slightly larger and allowing some dye to bleed onto bare wood. Lots of extra scraping and the line isn't as sharp.
- Wait until the dye is really dry before wiping off the tape residue with Naphtha. Otherwise it will cause the dye to bleed and smudge an otherwise sharp natural binding. More scraping.
Dyeing the Maple Top
PRS uses alcohol soluble wood dyes, so I did too. The forums suggested that lacquer thinner could be used in place of alcohol so I did that to avoid yet another purchase. I picked up a couple of disposable Preval spray units from Home Depot. I cleaned out a couple of glass jars (salsa and Snapple) to hold the mixed dyes and fashioned a funnel from a soda bottle.

I masked off the sides of the body completely including the natural binding leaving nothing but the top exposed. I built a new, standing paint boot from some cinder blocks and plywood. Those lessons are already paying off. I have a patent pending on the device used to support the body of the guitar which I like to call the Stack-O-Wood.

In order to enhance the grain of the maple top to give it a deeper look I decided to pre-dye using dark orange. The idea is to get a dark color into the grain of the wood (hence the need to strip off the sealer) then sand back to the bare wood leaving the color in the grain. From there I figure I'll finish it off with yellow for a sort of zebra-stripe look. After many coats of dye I had a decidedly orange guitar.

I let it dry overnight and began to sand back the color. I started to go for a sunburst type finish sanding more in the middle and less toward the edges. This didn't look like a sunburst fade so much as a half-sanded guitar body. From there I decided just to sand the whole thing.

It would seem that the grain didn't get all that much color. I feared that would happen since there is probably still plenty of sealer in the grain. Oh well, so much for my zebra-stripe finish. Another lesson learned.
Back to the paint booth, this time armed with both yellow and orange. Since not much orange remained after the pre-dye I figured I'd just layer yellow and orange and see what happens. It was difficult to see the color in my garage so I kept taking it outside until I liked the results.

After it dried I removed the masking tape to find some minor bleeding onto the natural binding. Good thing it's protected by the clear coat! I used an X-Acto knife to scrape away the extra color.

According to the Guitar ReRanch the dye would appear blotchy and dull until the clear coats are added. So far the finish is pretty vibrant. I can't wait to see it with clear coats!
The lessons learned this time aren't just from mistakes.
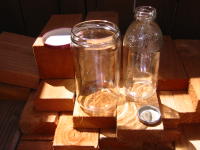

I masked off the sides of the body completely including the natural binding leaving nothing but the top exposed. I built a new, standing paint boot from some cinder blocks and plywood. Those lessons are already paying off. I have a patent pending on the device used to support the body of the guitar which I like to call the Stack-O-Wood.
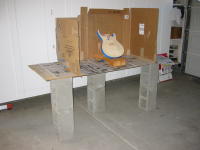

In order to enhance the grain of the maple top to give it a deeper look I decided to pre-dye using dark orange. The idea is to get a dark color into the grain of the wood (hence the need to strip off the sealer) then sand back to the bare wood leaving the color in the grain. From there I figure I'll finish it off with yellow for a sort of zebra-stripe look. After many coats of dye I had a decidedly orange guitar.
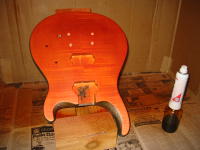

I let it dry overnight and began to sand back the color. I started to go for a sunburst type finish sanding more in the middle and less toward the edges. This didn't look like a sunburst fade so much as a half-sanded guitar body. From there I decided just to sand the whole thing.
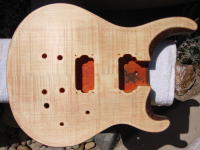

It would seem that the grain didn't get all that much color. I feared that would happen since there is probably still plenty of sealer in the grain. Oh well, so much for my zebra-stripe finish. Another lesson learned.
Back to the paint booth, this time armed with both yellow and orange. Since not much orange remained after the pre-dye I figured I'd just layer yellow and orange and see what happens. It was difficult to see the color in my garage so I kept taking it outside until I liked the results.

After it dried I removed the masking tape to find some minor bleeding onto the natural binding. Good thing it's protected by the clear coat! I used an X-Acto knife to scrape away the extra color.
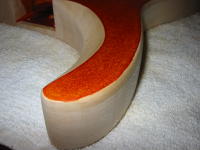

According to the Guitar ReRanch the dye would appear blotchy and dull until the clear coats are added. So far the finish is pretty vibrant. I can't wait to see it with clear coats!
The lessons learned this time aren't just from mistakes.
- Sanding off Saga sealer doesn't get it out of the grain.
- Layering dyes seems to make a nice iridescent finish.
- Including the beveled cut outs in the natural binding was a good idea!
Masking off the Natural Binding
PRS pioneered the use of "natural binding" on guitars. Instead of using an inlay around the top of the guitar a strip of wood is left free of color which looks like a natural wood binding.
This may be done by masking off the binding before adding color and removing it afterwards. However, some finish inevitably gets under the masking onto the raw wood which can be difficult to remove. Following the lead of those more experienced than myself I decided to mask off everything but the binding so I could protect it with some clear varnish before adding any color.
I carefully measured the depth of the binding around the top of the guitar using bits of tape to mark the depth.
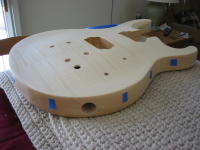
Masking the sides was pretty easy after that. I decided to include the two beveled cut outs in the binding for contrast. Masking them was a bit more effort but I'm sure it'll be worth it.

I set up a makeshift painting booth in my garage. I used lots of newspaper and drop cloths to protect everything. I stopped after four coats reasoning that this is just for protection not the final finish.
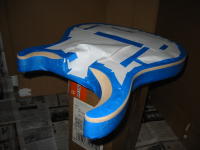
After it was dry I removed the masking tape. And now for today's lessons.
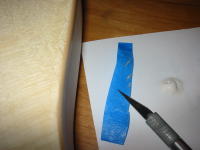
After carefully gluing the splinters back in place with some wood glue I was rather pleased with the result. Notice the darker stripe around the top edge.

This may be done by masking off the binding before adding color and removing it afterwards. However, some finish inevitably gets under the masking onto the raw wood which can be difficult to remove. Following the lead of those more experienced than myself I decided to mask off everything but the binding so I could protect it with some clear varnish before adding any color.
I carefully measured the depth of the binding around the top of the guitar using bits of tape to mark the depth.
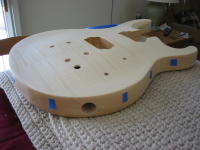
Masking the sides was pretty easy after that. I decided to include the two beveled cut outs in the binding for contrast. Masking them was a bit more effort but I'm sure it'll be worth it.

I set up a makeshift painting booth in my garage. I used lots of newspaper and drop cloths to protect everything. I stopped after four coats reasoning that this is just for protection not the final finish.
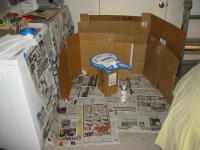
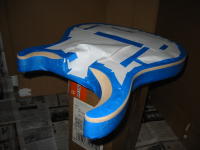
After it was dry I removed the masking tape. And now for today's lessons.
- If you've got a bad back don't set up a painting booth on the floor (duh).
- Remove the masking tape slowly. I managed to peel off a few splinters which were almost deep enough to expose the wood of the body beneath.
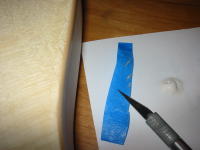
After carefully gluing the splinters back in place with some wood glue I was rather pleased with the result. Notice the darker stripe around the top edge.

Stripping the Sealer
It seems only fitting that a PRS style clone should have a PRS style finish. This means a deep, iridescent finish that seems to glow from within. Ok, perhaps a bit ambitious for a first project. And perhaps a bit unrealistic considering the quality of the maple top. In any case, I needed to get to the raw maple under that sealed finish.
After some research I decided on CitrusStrip which seemed less intimidating that some of the industrial-strength and highly toxic strippers out there. I got my supplies together and masked off some workspace with newspaper.

There are several things I learned soon afterward.
The stripping approach a failure I decided to get busy with some sand paper. More learning followed.
About two weekends after opening the box I finally had what would have to pass for bare wood. I would have stopped after sanding just the top but I ended up sanding through the sealer on the side so I just stripped off all of the sealer.
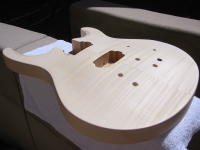
After all that work I was pleased to see some good flaming and that nice maple iridescence (which doesn't show in the pictures).
After some research I decided on CitrusStrip which seemed less intimidating that some of the industrial-strength and highly toxic strippers out there. I got my supplies together and masked off some workspace with newspaper.

There are several things I learned soon afterward.
- Strippers lift ink from newsprint very easily which doesn't so much protect an area as stain it. I made a second attempt by taping some plastic garbage bags to an outdoor table. Much better.
- Saga uses the most durable sealer known to man. After two applications of CitrusStrip there didn't seem to be any sign that the sealer would be leaving the wood any time soon.
- CitrusStrip may be more gentle than other strippers but it still burns like acid when it leaps over your glove onto your wrist. Soap and water works better than blowing on it going "Ow, ow, ow!".
The stripping approach a failure I decided to get busy with some sand paper. More learning followed.
- A carved-top body is not a good candidate for using a sanding block. I sanded through to the wood quickly in some areas and had to avoid them while sanding the rest of the top.
- Maple veneer is very thin. I came very close to sanding through the maple top when scrubbing off all of that sealer. The edges are particularly vulnerable.
About two weekends after opening the box I finally had what would have to pass for bare wood. I would have stopped after sanding just the top but I ended up sanding through the sealer on the side so I just stripped off all of the sealer.
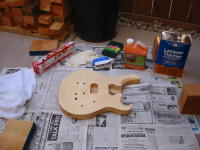
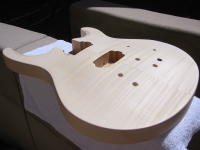
After all that work I was pleased to see some good flaming and that nice maple iridescence (which doesn't show in the pictures).
The Kit
My first impression of the kit is that it is better than what I had expected. It comes well packaged and includes everything needed to make the guitar. The body and neck are completely sealed so I could have put the thing together immediately and started playing. Don't think I wasn't tempted.

Looking closely there were small gaps in the 3-piece wood body, some filled, some not. The flamed maple top has some nice character but at about 1/16" thick it's no more than a veneer. Most of the hardware looks solid though I'll only really know the quality once I'm able to assemble it all and play it.


Looking closely there were small gaps in the 3-piece wood body, some filled, some not. The flamed maple top has some nice character but at about 1/16" thick it's no more than a veneer. Most of the hardware looks solid though I'll only really know the quality once I'm able to assemble it all and play it.
Finishing a Saga guitar kit (or, Experience is the best teacher)
I've considered buying an unfinished guitar as a project. However the only two choices I had were either a custom guitar -- too expensive for a first guitar finishing project -- or inexpensive Fender Stratocaster or Telecaster clones which just didn't interest me.
One day while browsing through guitar listings on eBay I happened across an auction for a Paul Reed Smith (PRS) clone kit by Saga (PS-10). It has a carved, flamed-maple top on a basswood body with a rosewood fretboard on a maple neck. It includes all of the (chrome) hardware right down to a cable, strings and a couple of picks. All for under $150 with shipping. Now we're talking.
After some searching I found the Guitar ReRanch, a site dedicated to guitar finishing. Besides offering basic instruction and finishing products, they also have discussion forums filled with everyone from first-timers like me to experts always willing to give advice. I also found this step-by-step walkthrough. I love the Internet.
After asking some preliminary questions in the forums I soon had the kit and about $100 in finishing supplies from the Guitar ReRanch.
One day while browsing through guitar listings on eBay I happened across an auction for a Paul Reed Smith (PRS) clone kit by Saga (PS-10). It has a carved, flamed-maple top on a basswood body with a rosewood fretboard on a maple neck. It includes all of the (chrome) hardware right down to a cable, strings and a couple of picks. All for under $150 with shipping. Now we're talking.
After some searching I found the Guitar ReRanch, a site dedicated to guitar finishing. Besides offering basic instruction and finishing products, they also have discussion forums filled with everyone from first-timers like me to experts always willing to give advice. I also found this step-by-step walkthrough. I love the Internet.
After asking some preliminary questions in the forums I soon had the kit and about $100 in finishing supplies from the Guitar ReRanch.